¿Sabes cómo eliminar todo lo que no aporta nada a tu producto? La metodología Lean manufacturing te brinda herramientas para conseguirlo y optimizar tu producción.
Lo increíble de la metodología Lean Manufacturing ─o manufactura esbelta en español─ es que se puede aplicar a casi cualquier flujo de trabajo o cadena de producción, sin importar el sector de la empresa que comienza a utilizarla.
Hay que recordar que el propósito principal de la Lean Production es minimizar los desperdicios de cualquier tipo, ya sea de mercancía, maquinaria, tiempo, dinero, etc. Y aunque este concepto nació desde 1950 o poco antes, hoy para llevarlo a cabo, es indispensable estar familiarizado con las herramientas de la industria 4.0: indicadores OEE, torretas ANDON, redes industriales y más.
Sin duda, con dispositivos digitales y el famoso industrial internet of things (IIoT) ahora es relativamente fácil identificar los desperdicios en un proceso de fabricación, pero aún antes de que existieran estas soluciones, la metodología Lean Manufacturing tenía muy claras las áreas que debían atacarse.A continuación, se presentan los ocho desperdicios de la manufactura esbelta:
1- Defectos:
Un producto con defectos es pérdida de tiempo, de material y de dinero. Esto a su vez, baja los estándares de calidad y puede ocasionar la insatisfacción del cliente al no ser detectado.
Para que la maquinaria alerte sobre fallos, e incluso pare la producción para no obtener una gran cantidad de piezas con desperfectos, son ideales herramientas como las torretas ANDON y sistemas OEE.
2- Sobreproducción:
Depende del tipo de producto, pero en algunos casos el producir más de lo demandado, ocasionará pérdidas si se habla de alimentos con fecha de caducidad. Si se trata de objetos, es probable que se guarden en algún almacén y empiecen a deteriorarse con el paso del tiempo.
Utilizar estadísticas y medición industrial para conocer al mercado, será de gran ayuda para tener clara la cantidad de producto que se debe fabricar.
3- Inventario:
Uno de los principios de Lean Manufacturing es precisamente evitar la sobreproducción, para no tener llenos los depósitos. El exceso de stock por lo general provoca un mal inventario, ya que contabilizar y buscar productos específicos resulta mucho más difícil con almacenes en su máxima capacidad.
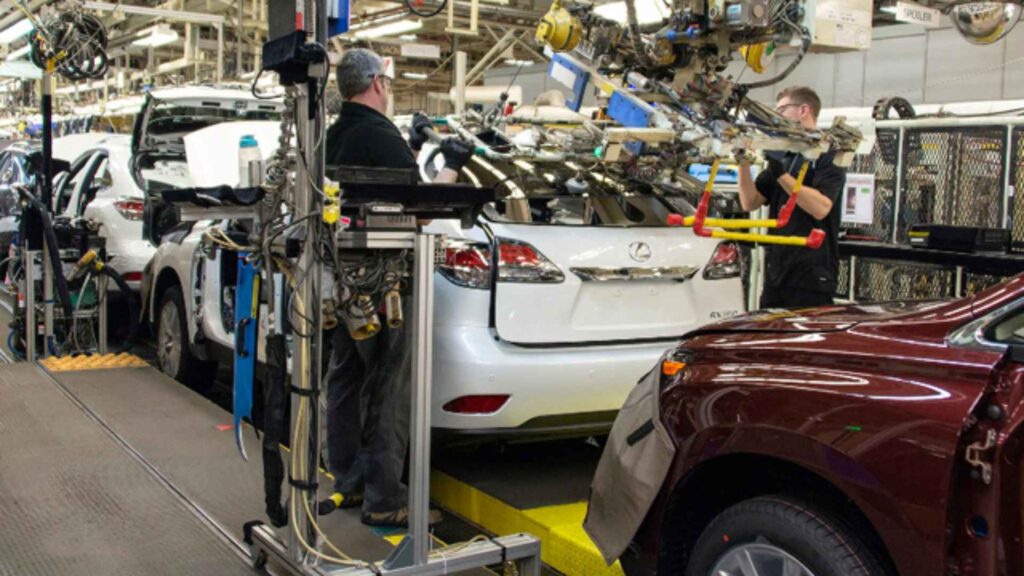
4- Desperdicio de talento:
Aunque algunas personas piensan que la automatización de procesos lleva a eliminar puestos de trabajo, lo cierto es que la industria 4.0 ha creado empleos diversos, con la aparición de nuevas herramientas que se encargan de lo más simple. Un empleado seguro estará más motivado al ser capacitado para funciones más complejas, dejando de lado procesos rutinarios.
Es importante recordar que si un trabajador no se siente valorado y realiza tareas que no van de acuerdo a su capacidad, buscará una mejor oportunidad en otra empresa.
5- Transporte excesivo:
Sucede cuando los productos pasan mucho tiempo siendo transportados y se estropean o dañan. No solo se perderá tiempo en traslados innecesarios, si no que se puede perder la mercancía en su totalidad. Lo ideal es hacer una gestión de material y organización adecuada de rutas lo más directas posibles.
6- Procesamiento de más:
En la manufactura esbelta el proceso de producción debe estar bien pensado para no ser redundante, es decir, que su diseño no sea el mejor para reducir tiempos. En especial en esta etapa, la industria 4.0 brinda la oportunidad de eliminar codificación manual en la maquinaria, lo que hará una enorme diferencia en los resultados finales.
7- Movimiento:
Aquí se habla del movimiento de las personas. Una fábrica que no cuenta con dispositivos digitales y torretas ANDON o sistemas OEE, es un lugar donde los empleados deben ir de un punto a otro durante todo el día. En cambio, se ahorrará tiempo al poder monitorear todo con herramientas y redes industriales (además de no agotar en vano a los trabajadores).
8: Espera:
Una empresa que espera por personas, materiales, documentos y más, está condenada a perder tiempo. Esperar a que termine una parte del proceso para empezar otro, también afecta el flujo de trabajo (claro que hay excepciones, pues en algunos casos es necesario).
Las soluciones de la industria 4.0 que hacen simples las autorizaciones, automatizan tareas manuales y están al alcance de todo el equipo de trabajo, son herramientas de Lean Manufacturing que marcarán la diferencia en una cadena de producción.
En ANK podemos ayudarte a no tener más desperdicios a través de la conectividad industrial. ¡Solicita información sobre nuestros servicios!