Al buscar el nacimiento de la metodología Lean Manufacturing, también conocida como Lean Production, se deben mencionar dos nombres: Henry Ford y F.W. Taylor. Los padres del automóvil moderno fueron pioneros en introducir mejoras a sus procesos de fabricación y optimizar la producción en serie. De este primer acercamiento, que sucedió a principios del siglo XX en Estados Unidos, hay que viajar hasta Japón. Es aquí donde el método realmente se consolidó con éxito.
Sakichi Toyoda y su hijo Kiichiro podrían ser considerados los padres de la metodología Lean Manufacturing. Ambos fundadores del Grupo Toyota, fueron responsables de inventar un dispositivo llamado Jidoka, el cual detectaba incidencias y problemas de calidad en los telares. Además de lanzar una advertencia cuando había un error, la máquina era capaz de parar la producción para evitar la manufactura de productos defectuosos.
Después de obtener excelentes resultados con su innovación, Sakichi Toyoda logró vender miles de telares que no solo ahorraban tiempo y dinero, sino que también permitían que un solo trabajador operara varias máquinas.
De padre e hijo nacieron filosofías y conceptos que siguen vigentes al día de hoy: el método Just in Time, que apuesta por una combinación perfecta de instalaciones, máquinas y personas para mejorar la producción; y el Toyota Production System, un modelo que se basaba en manufacturar solo lo que el cliente solicita. Por último, también crearon el Total Production Maintenance y su Overall Equipment Effectiveness (OEE) con la colaboración del ingeniero Seiichi Nakajima. Este concepto es uno de los principales servicios en ANK y se explica con más detalle en otro artículo de este blog.
El proceso único de Toyota fue imposible de igualar por el resto de la industria japonesa. Esto hizo que el Gobierno de Japón implementara “El modelo Toyota” en todas las empresas posibles, llevando al país a un crecimiento sin precedentes en la última parte del siglo XX.
Sin embargo, la metodología Lean Manufacturing no llegaría a Occidente hasta los años noventa, gracias a la publicación del libro “The Machine that Changed the World: The Story of Lean Production, Toyota’s Secret Weapon in the Global Car Wars that is now Revolutionizing World Industry” de los autores Wornak, Jones y Roos.
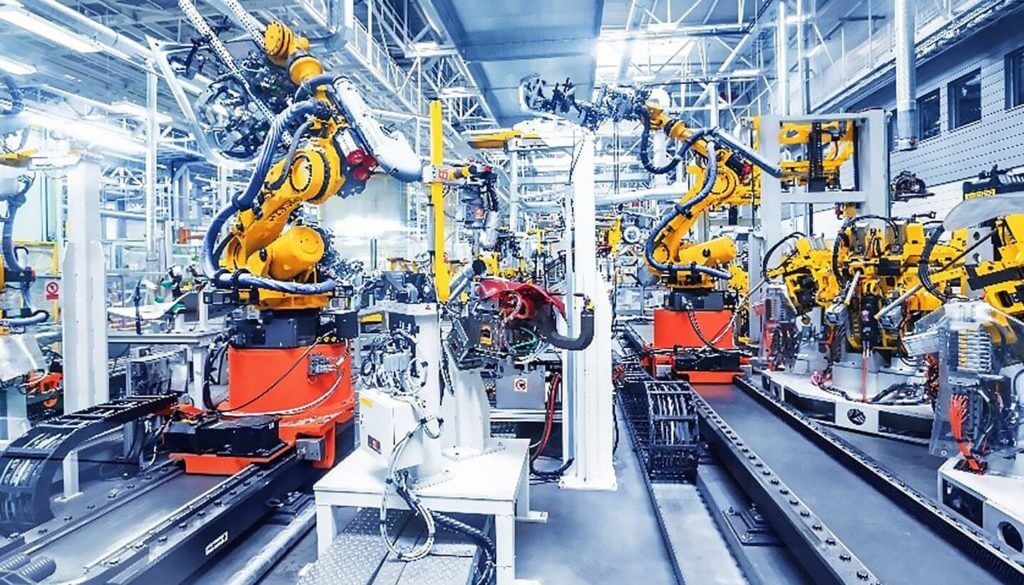
La metodología Lean Manufacturing en la actualidad
Optimizar los sistemas de producción, reducir los desperdicios y lograr que personas y máquinas trabajen de forma sincronizada son algunos de los propósitos de la metodología Lean Manufacturing. En la actualidad, el sistema de Toyota se aplica y se adapta a todo tipo de empresas a nivel mundial. Su expansión a diversos sectores ha generado nuevos conceptos como Lean Health, Lean Construction y Lean Office, entre otros.
Si hay que mencionar beneficios que ofrece la metodología a la industria manufacturera en México y a nivel internacional, los más relevantes serían:
- Reducción considerable en los tiempos de entrega.
- Menor gasto en la producción.
- Aumento general en la productividad.
- Mejoría en la calidad del producto.
- Reducción en inventario y stock de los productos.
- Menos desperdicios en el proceso.
Un elemento vital de la metodología Lean Manufacturing al día de hoy son los Sistemas Andon, que se utilizan para alertar de manera visual sobre posibles errores en la producción. Funciona de una forma bastante sencilla: una columna de luces con varios colores ─por lo regular verde, amarillo y rojo─ que se iluminará dependiendo de si hay falla o no. Estos sistemas son capaces de parar las máquinas y restaurar la manufactura cuando el problema ha sido arreglado.
Entre compañías exitosas que utilizan la metodología Lean Manufacturing con éxito están Nike, Intel, John Deere y por supuesto, Toyota. Si tu empresa forma parte de la industria manufacturera en México y buscas optimizar tus procesos de fabricación y producción, ¡ANK puede ayudarte a encontrar la mejor solución! Solicita información sobre los distintos servicios que tenemos para ti.